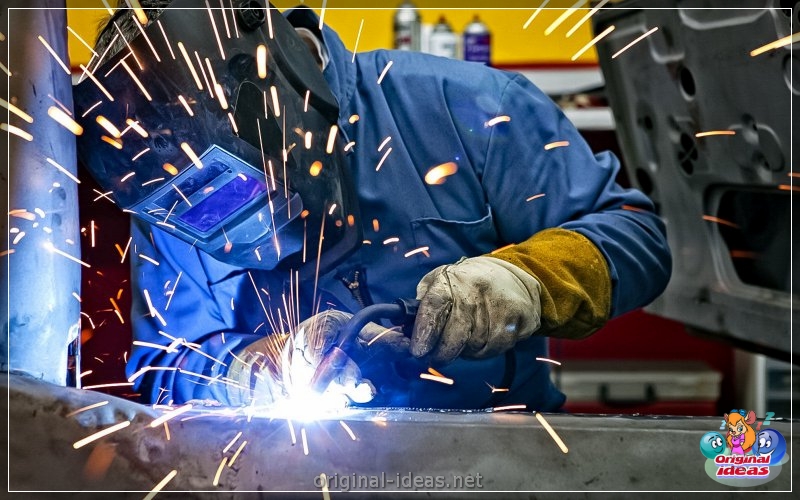
Since the welding flame should create a temperature exceeding three thousand degrees in the melting zone of metals, acetylene and oxygen are used as a fuel material for the burner. The welded connection is created without the use of effort, only due to hardening of the molten metal.
Gas welding finds enough use for welding cast iron, non -ferrous metals. In these cases, gas mixtures for welding from /Katalog /Svarochnye-Smesi may consist of a mixture of oxygen and methane, oxygen and propanbutan mixture, oxygen and oil gas.
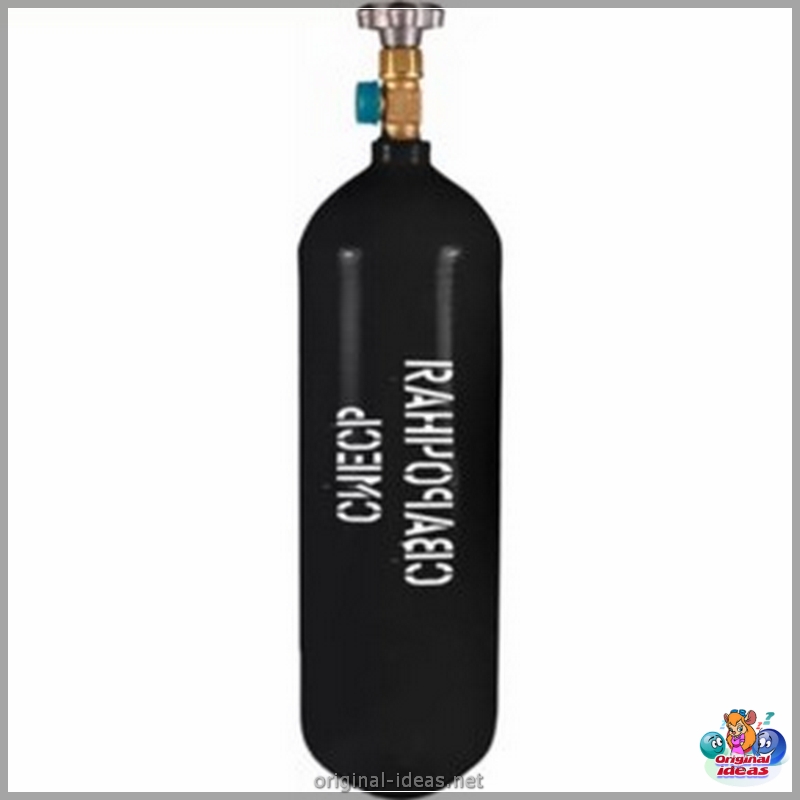
Welding can be carried out both by melting the welded parts, and with the introduction of a mourned metal of the filler rod. In this case, the flames of the welding burner melt the edges of the parts welded and the metal of the molten filler rod is added to the molten metal. This is done with continuous movement along the weld with the commission of fast transverse movements, which ensure rawar and the correct distribution of filler material.
According to the mutual location of the filler rod and welding burner, as well as the direction of their movement, gas welding can be left or right. With left welding, a welding burner and a filler twig move from right to left, leaving a welding seam behind the burner. With the right method of welding, the burner and the filler twig move from left to right, the welded seam is in front of the burner. Left welding is used when connecting thin steel sheets and non -ferrous metal products. When welding metal with a thickness of five millimeters, it is preferable to use right welding. At the same time, the performance and efficiency of welded work increases, the welding seam is higher than the quality.
Gas welding has found its use when sailing solid metals. With this welding method, cast iron designs are welded. Cast iron parts before welding are heated to six hundred degrees, and after welding they slowly cool under thermal insulation. If you use brass or bronze as a filler bar when welding cast iron, you can weld without heating the blanks.